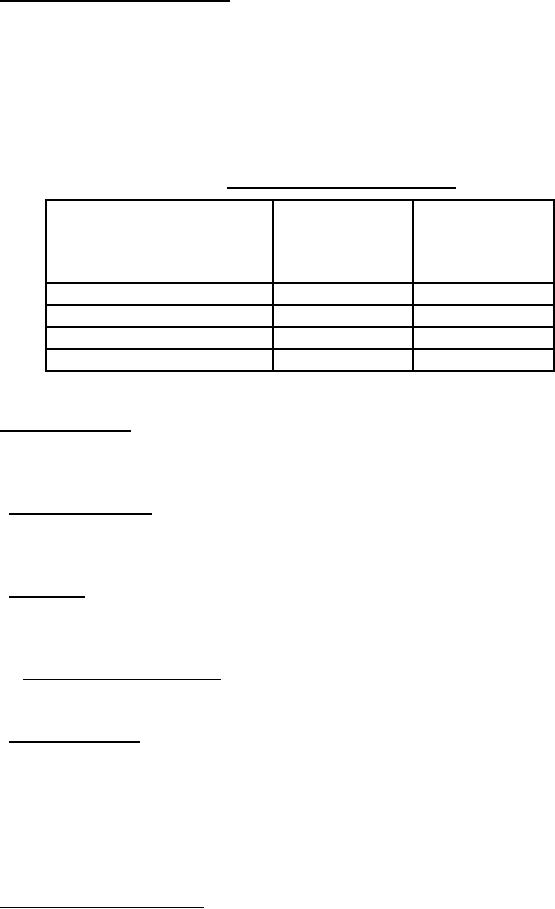
MIL-PRF-52666F
3.8 Government-furnished property. The Government shall furnish the number of filter-
coalescer elements and separator stages shown in table II for each F/S in the contract or purchase
order (see 6.10). Half of the filter-coalescer elements furnished for each F/S shall be installed in
the F/S, and half shall be shipped with each F/S as replacements. When a first article inspection
is specified (see 6.2), an additional set or sets of filter-coalescer elements shall be furnished by
the Government to support testing. If a manufacturer requires a different number of filter-
coalescer elements than specified in table II, the contracting officer shall be notified.
TABLE II. Government-furnished property.
Filter/Separator Type
NUMBER OF
NUMBER OF
F-C ELEMENTS
SEPARATOR
FURNISHED
STAGES
FURNISHED
Type I
2
1
Type II (Both Classes)
8
4
Type III
10
5
Type IV
36
18
3.9 Interchangeability. All components and parts having the same manufacturer's part
number shall be functionally and dimensionally interchangeable and shall be replaceable with
each other with respect to installation and performance.
3.10 Human engineering. Human engineering criteria, principles and practices (see 6.11)
shall be considered as part of the F/S. For example, the F/S shall be capable of being transported
and operated by 5th through 95th percentile military personnel wearing gloves or mittens.
3.11 Reliability. When specified (see 6.2), the F/S shall decontaminate military fuels to the
cleanliness level specified herein for at least 20 hours per day, with four hours per day allowed
for scheduled and unscheduled maintenance and repair.
3.11.1 Mean-time-between-failure. The specified mean-time-between-failure (MTBF) shall
be 140 hours when the F/S is operated at rated capacity and tested as specified in 4.5.2.8.
3.12 Maintenance ratio. The F/S should have a maintenance ratio of not greater than 0.03.
Maintenance ratio is defined as the ratio of the total active maintenance man-hours required
(scheduled and unscheduled) to the total operating time. Man-hours for repair of replaced
components, and scheduled before-and-after-operation checks are excluded. A maintenance
schedule shall be established prior to start of any testing.
4 VERIFICATION
4.1 Classification of inspections. The inspection requirements specified herein are classified
as follows:
7
For Parts Inquires submit RFQ to Parts Hangar, Inc.
© Copyright 2015 Integrated Publishing, Inc.
A Service Disabled Veteran Owned Small Business